Super beautiful stainless steel etching!
Check this out!
Gorgeous stainless steel etching!
Let’s take a close look at it.
Welcome to the long-lost stainless steel popularization of science! We consulted with some specialists and worked overtime to sort out the information about this topic. Finally, this popular science articles about stainless steel etching process are grand present. Let’s have a look!
Stainless steel etching plates are common /(conventional) materials for elevator decoration, such as hall doors, car doors, car walls, nameplate surfaces, etc., which we are often seen. , which can be seen often by us. However, most people don't know how it is they processed. This article briefly introduces some related knowledge, and we hope you can have to bring a deeper understanding of this process.
Generally, the term "photochemical etching" refers to the removal of the protective film from the etched area after exposure process, and the contact with the chemical solution during etching to achieve the effect of dissolution and corrosion, thereby forming the effect of unevenness or hollowing.
The etching stainless steel plate used in the elevator usually uses the screen printing method. It can be customized with individual patterns, characters and logos. It is often usually used in the elevator hall door, cabin and car wall. It’s commonly used in elevator decoration(It’s common material for elevator decoration). The etching stainless steel plate usually used 304 stainless steel as a substrate, can be used for process as a mirror, hairline, and grain plate etching, and supplemented by sandblasting, concave gold, gold plating, etc., as well as a combination of various effects and processes to achieve a colourful expression.
Process Flow/Technical Process
1:Exposure method:
The project is based on the drawing to prepare the material size - material preparation - material cleaning - drying → filming or coating → drying → exposure → development → drying - etching → stripping → Finished
2:Screen printing:
Cutting → cleaning plate (stainless steel/ other metal materials) → screen printing → etching → release film → Finished
Advantage:
The biggest advantage of stainless steel etching plates is their resistance to corrosion, pitting, rust or wear, so the structural integrity of the components can be permanently maintained.
From the splendid Shanghai Jinmao Tower, the Petronas Twin Towers, the all-stainless steel casings Los Angeles Disney Concert Hall with all-stainless steel casings, and to the London Waterloo Railway Station in London, England. From the 150,000-square-meter roof, the 452-meter-tall tower, to the exquisite trim and structural parts. this is These all evidenced by the contribution of coloured stainless steel etching plates to sustainable buildings. It is the most sustainable building material and exudes unique charms that are not found in general materials around the world.
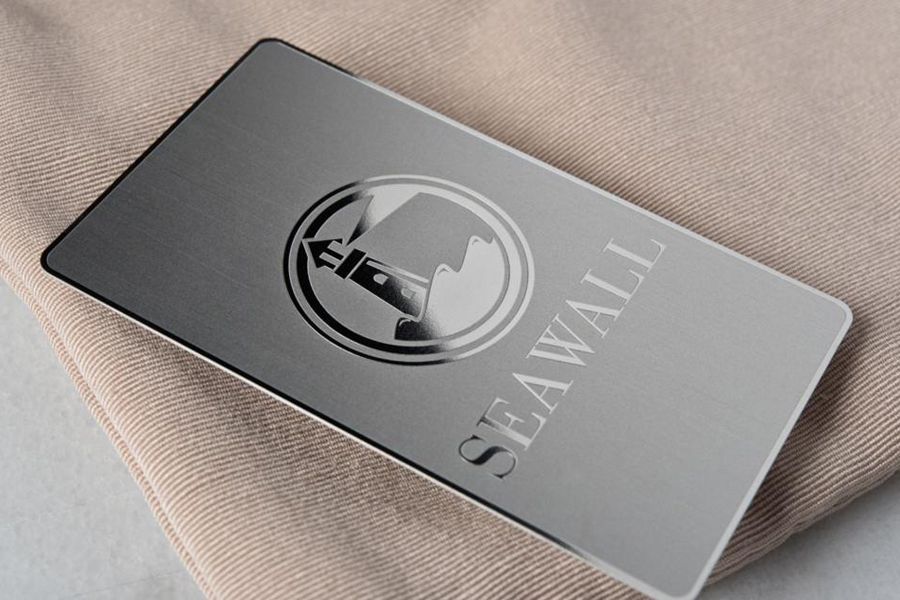
Firstly, the most sustainable construction of stainless steel etching plates should have a designed life of at least 50 years. In most sustainable building designs, main parts of the building, such as structural frames, roofs, walls and other large surfaces, are required to have the same life as the building structure, avoiding the use of coatings and generating emissions and increasing the impact of the building's environmental footprint methods improve the positive impact to ecological footprint. If the right stainless steel is chosen and with properly maintained, the coloured stainless steel can never be replaced never need to be replaced during the in the whole life of the building, if the building even it lasts for hundreds of years. At the same time, it is not necessary to carry out a coating treatment on the surface of the stainless steel in order to prevent corrosion.
Secondly, the best materials can either be refurbished naturally or recycled to maintain the same stainless steel etching plate quality.
Stainless steel etching plate have has the highest material composition available in many constructions. If They are fully recyclable when if they reach a certain service life, they can be recycled to produce the same quality stainless steel etching plates of the same quality.
Attention Problems:
Reduce lateral erosion and protuberant edge, increase the etching coefficient
The lateral erosion creates a protuberant edge. Usually, the longer the printed board is in the etchant, the more serious lateral erosion is (or with use the old-fashioned left and right swing etchers). Lateral erosion seriously affects the accuracy of printed conductors, and severe side etching will make it impossible to make fine wires. When lateral erosion and the protuberant edge is reduced, the etch coefficient increased, and a high etch coefficient indicates there is an ability to maintain a thin wire, making the etched wire close to the original size.
Improve the etch rate consistency between the plates
In a continuous plate etch, the more consistent the etch rate, the more uniformly etched the plate. To achieve this requirement, it must be ensured that the etchant remains in an optimal etched state throughout the etching process. This requires the selection of an etchant that is easily regenerated and compensated for easy control of the etch rate. Processes and equipment that provide constant operating conditions and automatic control of various solution parameters are selected. This is achieved by controlling the amount of dissolved copper, the pH, the concentration of the solution, the temperature, the uniformity of the solution flow rate (spray system or nozzle and the oscillation of the nozzle), and the like soon.
Improve the uniformity of the etch rate throughout the entire plate surface
The uniformity of etching on the upper and lower sides of the plate and the various parts of the plate is determined by the uniformity of the flow rate of the etchant on the surface of the plate.
During the etching process, the etching rates of the upper and lower plates are often inconsistent. Generally, the etch rate of the lower plate surface is higher than that of the upper plate surface. Because of the accumulation of solution on the upper plate surface, the progress of the etching reaction is weakened. The phenomenon of uneven etching of the upper and lower plates can be solved by adjusting the spray pressure of the upper and lower nozzles. A common widespread problem of etched printed plates is that it’s difficult to etch all of the plates at the same time, and the edges of the plates are etched faster than the centre of the board. ItThere is an effective measure to use a sprinkler system and to oscillate the nozzle. Further improvement can be achieved by making the spray pressure different of the at the centre of the plate and the edge of the plate different, the front edge of the plate and the back end of the plate intermittently etching to achieve uniform etching of the entire surface.
Improve the ability to safely handle and etch thin copper foils and thin laminates
When etching a thin laminate such as an inner layer of a multilayer plate, the plate is easily wound on the roller and the transfer wheel to cause waste. Therefore, the equipment for etching the inner layer must ensure smooth and reliable handling of the thin laminate. Many equipment manufacturers add gears or rollers to the etching machine to prevent this from happening. A The better method is to use an additional left and right rocking Teflon coated wire as a support for the transfer of thin laminates. For etching of thin copper foil (eg 1/2 or 1/4 ounce), it must be guaranteed not to be scratched. The thin copper foil can’t withstand the mechanical drawbacks of etching 1 ounce of copper foil, and sometimes more intense vibration can scratch the copper foil.
Reduce pollution:
When to use etching? Using etching under what circumstances?
△ 1:
The shape of the metal parts to be processed is complicated The metal part to process with a complicated shape. For example, such as a very thin stainless steel mesh is a typical example. By using etching techniques, moulding difficulties and processing costs can be reduced.
△ 2:
If your product is very thin (between 0.03mm and -1mm), use other processes technology may cause the product to deform. The etching ensures that the product is not deformed not deformation. In general, the thinner the product is, the higher the precision is.
△ 3:
The etching process does not change the physical properties such as hardness, strength, and formability of the metal material.
△ 4:
Some metal materials are easily broken during the stamping process and are prone to curling of the burrs, which affects the assembly of the product, and the etching ensures that the materials are intact.
△ 5:
Magnetic soft materials can retain their original physical properties after etching.
△ 6:
The etched product has no burrs.
Cleaning and surface treatment of the substrate (for small etched workpieces of stainless steel, the coating process can be completed directly by screen printing. But, for large areas, stainless steel etching products that cannot be performed by silk screen can only be produced by the way of coating development.)---->Coating---->Hot air pre-baking---->Exposure---->Development---->Complementary light curing---->Dry---->etching off Ink---->post-production---->inspection---->package shipment.
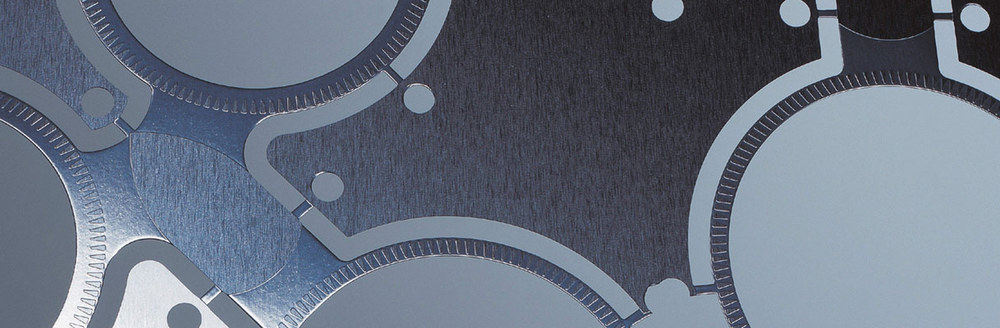
------------------------------------------------------------------------------------- stainless steel etching---------------------------------------------------------------------------------------------
Check this out!
Gorgeous stainless steel etching!
Let’s take a close look at it.
Welcome to the long-lost stainless steel popularization of science! We consulted with some specialists and worked overtime to sort out the information about this topic. Finally, this popular science articles about stainless steel etching process are grand present. Let’s have a look!
Generally, the term "photochemical etching" refers to the removal of the protective film from the etched area after exposure process, and the contact with the chemical solution during etching to achieve the effect of dissolution and corrosion, thereby forming the effect of unevenness or hollowing.
The etching stainless steel plate used in the elevator usually uses the screen printing method. It can be customized with individual patterns, characters and logos. It is often usually used in the elevator hall door, cabin and car wall. It’s commonly used in elevator decoration(It’s common material for elevator decoration). The etching stainless steel plate usually used 304 stainless steel as a substrate, can be used for process as a mirror, hairline, and grain plate etching, and supplemented by sandblasting, concave gold, gold plating, etc., as well as a combination of various effects and processes to achieve a colourful expression.
Process Flow/Technical Process
1:Exposure method:
The project is based on the drawing to prepare the material size - material preparation - material cleaning - drying → filming or coating → drying → exposure → development → drying - etching → stripping → Finished
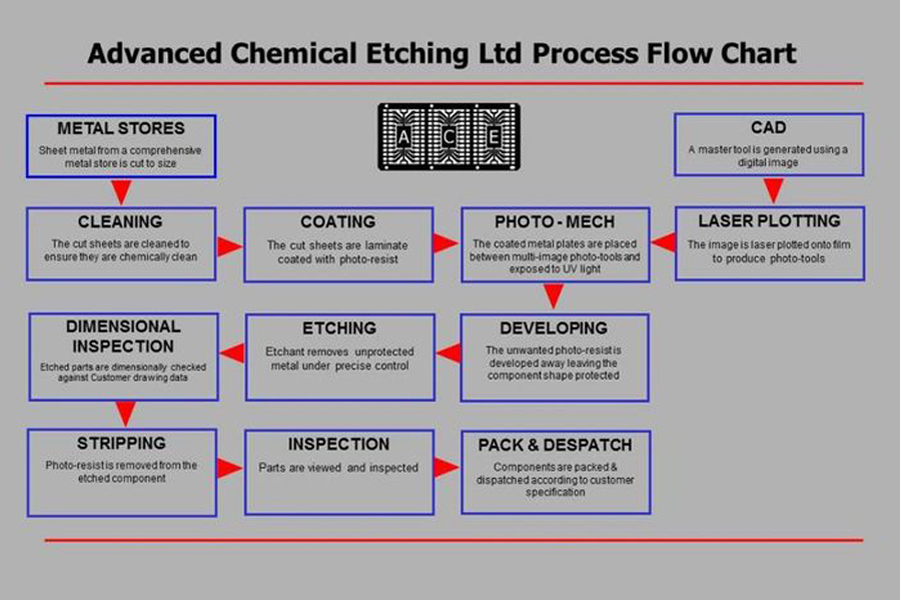
2:Screen printing:
Cutting → cleaning plate (stainless steel/ other metal materials) → screen printing → etching → release film → Finished
Advantage:
The biggest advantage of stainless steel etching plates is their resistance to corrosion, pitting, rust or wear, so the structural integrity of the components can be permanently maintained.
From the splendid Shanghai Jinmao Tower, the Petronas Twin Towers, the all-stainless steel casings Los Angeles Disney Concert Hall with all-stainless steel casings, and to the London Waterloo Railway Station in London, England. From the 150,000-square-meter roof, the 452-meter-tall tower, to the exquisite trim and structural parts. this is These all evidenced by the contribution of coloured stainless steel etching plates to sustainable buildings. It is the most sustainable building material and exudes unique charms that are not found in general materials around the world.
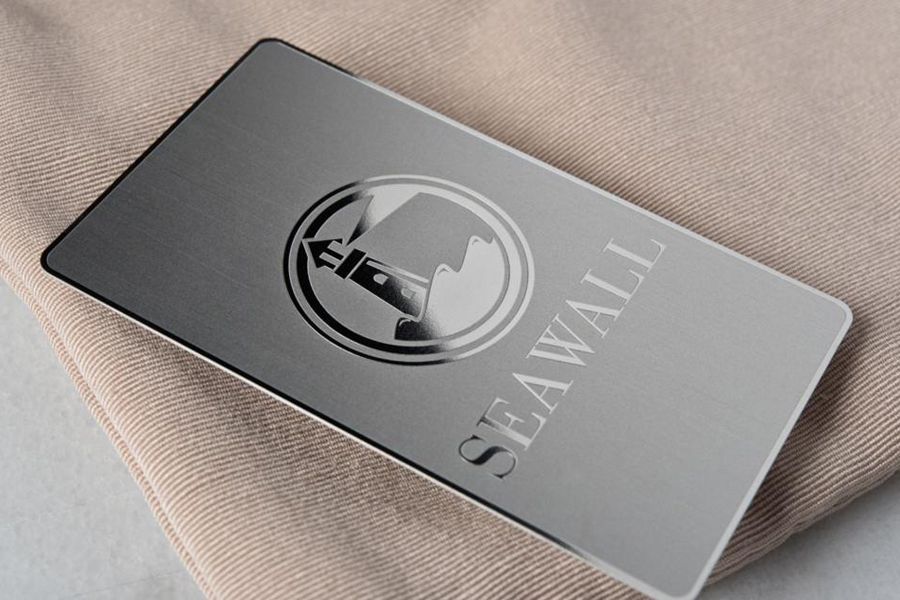
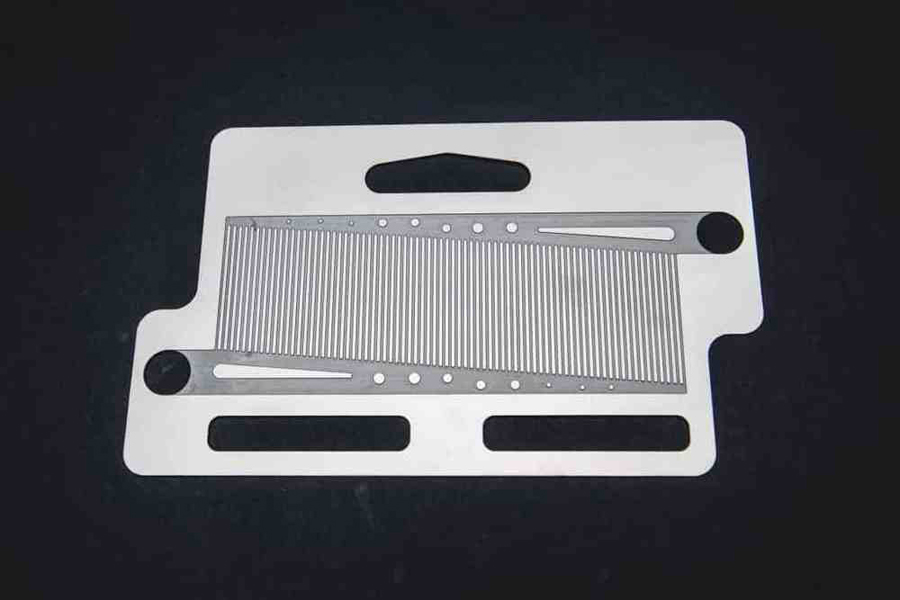
Firstly, the most sustainable construction of stainless steel etching plates should have a designed life of at least 50 years. In most sustainable building designs, main parts of the building, such as structural frames, roofs, walls and other large surfaces, are required to have the same life as the building structure, avoiding the use of coatings and generating emissions and increasing the impact of the building's environmental footprint methods improve the positive impact to ecological footprint. If the right stainless steel is chosen and with properly maintained, the coloured stainless steel can never be replaced never need to be replaced during the in the whole life of the building, if the building even it lasts for hundreds of years. At the same time, it is not necessary to carry out a coating treatment on the surface of the stainless steel in order to prevent corrosion.
Secondly, the best materials can either be refurbished naturally or recycled to maintain the same stainless steel etching plate quality.
Stainless steel etching plate have has the highest material composition available in many constructions. If They are fully recyclable when if they reach a certain service life, they can be recycled to produce the same quality stainless steel etching plates of the same quality.
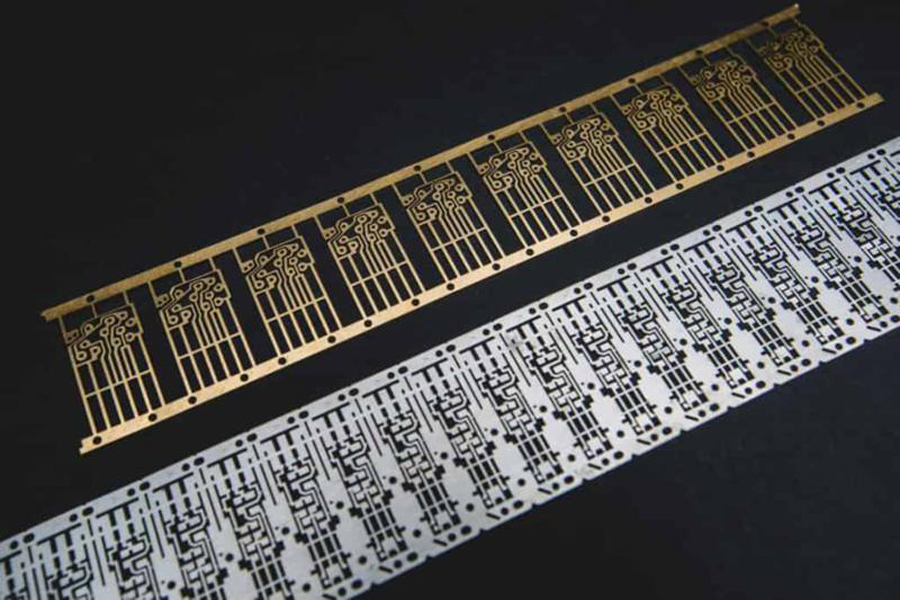
Attention Problems:
Reduce lateral erosion and protuberant edge, increase the etching coefficient
The lateral erosion creates a protuberant edge. Usually, the longer the printed board is in the etchant, the more serious lateral erosion is (or with use the old-fashioned left and right swing etchers). Lateral erosion seriously affects the accuracy of printed conductors, and severe side etching will make it impossible to make fine wires. When lateral erosion and the protuberant edge is reduced, the etch coefficient increased, and a high etch coefficient indicates there is an ability to maintain a thin wire, making the etched wire close to the original size.
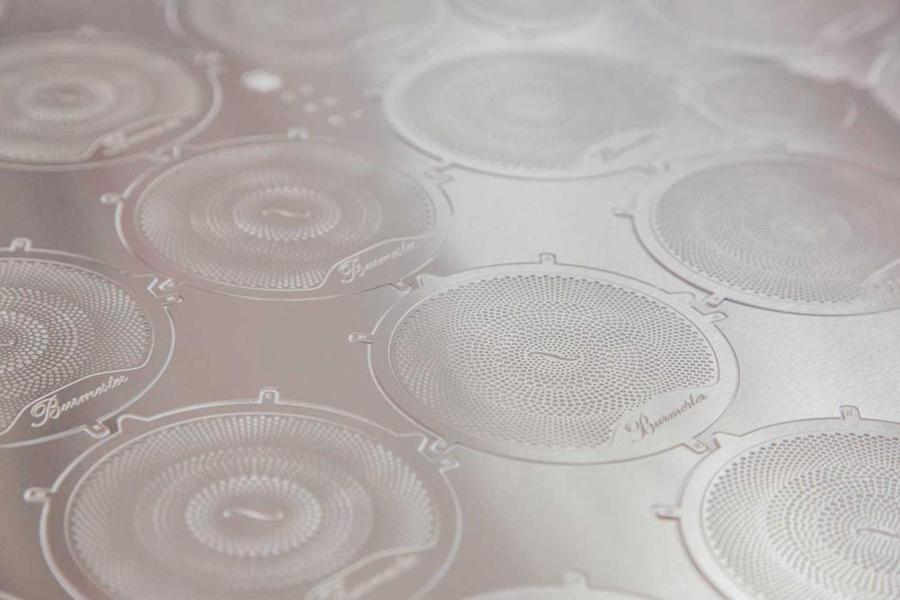
Improve the etch rate consistency between the plates
In a continuous plate etch, the more consistent the etch rate, the more uniformly etched the plate. To achieve this requirement, it must be ensured that the etchant remains in an optimal etched state throughout the etching process. This requires the selection of an etchant that is easily regenerated and compensated for easy control of the etch rate. Processes and equipment that provide constant operating conditions and automatic control of various solution parameters are selected. This is achieved by controlling the amount of dissolved copper, the pH, the concentration of the solution, the temperature, the uniformity of the solution flow rate (spray system or nozzle and the oscillation of the nozzle), and the like soon.
Improve the uniformity of the etch rate throughout the entire plate surface
The uniformity of etching on the upper and lower sides of the plate and the various parts of the plate is determined by the uniformity of the flow rate of the etchant on the surface of the plate.
During the etching process, the etching rates of the upper and lower plates are often inconsistent. Generally, the etch rate of the lower plate surface is higher than that of the upper plate surface. Because of the accumulation of solution on the upper plate surface, the progress of the etching reaction is weakened. The phenomenon of uneven etching of the upper and lower plates can be solved by adjusting the spray pressure of the upper and lower nozzles. A common widespread problem of etched printed plates is that it’s difficult to etch all of the plates at the same time, and the edges of the plates are etched faster than the centre of the board. ItThere is an effective measure to use a sprinkler system and to oscillate the nozzle. Further improvement can be achieved by making the spray pressure different of the at the centre of the plate and the edge of the plate different, the front edge of the plate and the back end of the plate intermittently etching to achieve uniform etching of the entire surface.
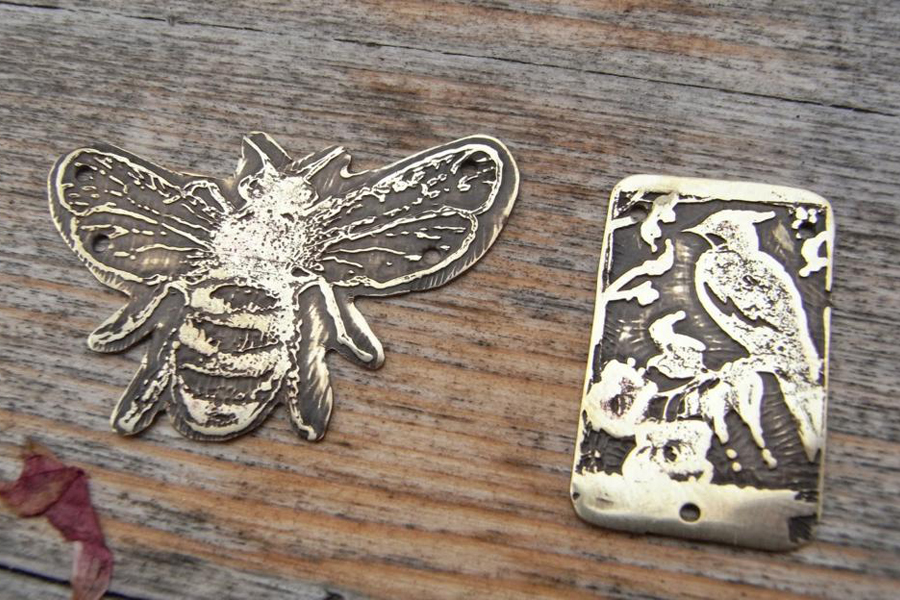
Improve the ability to safely handle and etch thin copper foils and thin laminates
When etching a thin laminate such as an inner layer of a multilayer plate, the plate is easily wound on the roller and the transfer wheel to cause waste. Therefore, the equipment for etching the inner layer must ensure smooth and reliable handling of the thin laminate. Many equipment manufacturers add gears or rollers to the etching machine to prevent this from happening. A The better method is to use an additional left and right rocking Teflon coated wire as a support for the transfer of thin laminates. For etching of thin copper foil (eg 1/2 or 1/4 ounce), it must be guaranteed not to be scratched. The thin copper foil can’t withstand the mechanical drawbacks of etching 1 ounce of copper foil, and sometimes more intense vibration can scratch the copper foil.
Reduce pollution:
When to use etching? Using etching under what circumstances?
△ 1:
The shape of the metal parts to be processed is complicated The metal part to process with a complicated shape. For example, such as a very thin stainless steel mesh is a typical example. By using etching techniques, moulding difficulties and processing costs can be reduced.
△ 2:
If your product is very thin (between 0.03mm and -1mm), use other processes technology may cause the product to deform. The etching ensures that the product is not deformed not deformation. In general, the thinner the product is, the higher the precision is.
△ 3:
The etching process does not change the physical properties such as hardness, strength, and formability of the metal material.
△ 4:
Some metal materials are easily broken during the stamping process and are prone to curling of the burrs, which affects the assembly of the product, and the etching ensures that the materials are intact.
△ 5:
Magnetic soft materials can retain their original physical properties after etching.
△ 6:
The etched product has no burrs.
Cleaning and surface treatment of the substrate (for small etched workpieces of stainless steel, the coating process can be completed directly by screen printing. But, for large areas, stainless steel etching products that cannot be performed by silk screen can only be produced by the way of coating development.)---->Coating---->Hot air pre-baking---->Exposure---->Development---->Complementary light curing---->Dry---->etching off Ink---->post-production---->inspection---->package shipment.
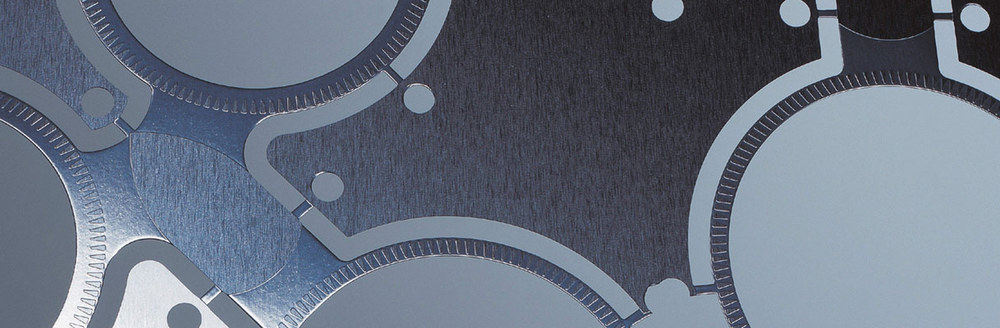
------------------------------------------------------------------------------------- stainless steel etching---------------------------------------------------------------------------------------------