Most of the ventilation purification devices of Chinese nuclear plants are made by Austenitic stainlesssteel.
The ventilation purification device of nuclear power plant functions in the air supply and exhaust system, which can install with different types of air filter units according to the actual working conditions.
If it is used to purify the air, which is suitable for the air supply and exhaust system used on polluted or harmful air, it can protect the staff’s safety and the sanitation of the environment.
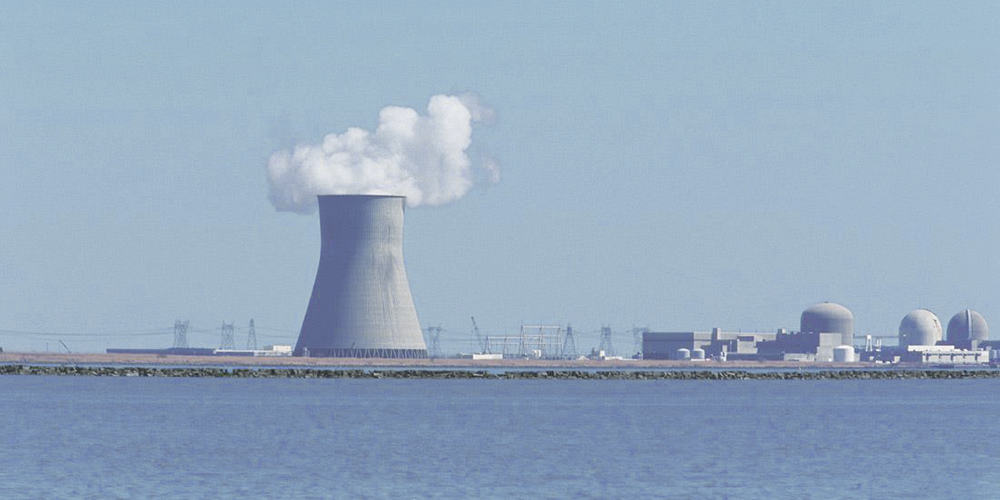
Austenitic stainless steel has a good performance on corrosion resistance and radiation resistance.Nuclear power plant tends to be built in the coastal area where it is of high humidity and salt content in the air and chloride ion is one of the main causes of corrosion of stainless steel.
For the safety of the ventilation purification system of a nuclear power plant, it is crucial to improve the corrosion resistance of Austenitic stainless steel.
Comparisons among Austenitic Stainless Steel Materials:
At normal temperature and low temperature, Austenitic stainless steel has strong toughness,plasticity, and weldability as well as corrosion resistance, such as chemical and electrochemical corrosion resistance.
304 stainless steel is general stainless steel, which is widely used in devices and machines that require good overall performance like corrosion resistance and formability. 304 stainless steel is provided with good corrosion resistance and intergranular corrosion resistance.
304L stainless steel is a variant of 304 stainless steel, which is in lower carbon content, typically suitable for being welded. When the stainless steel is near to the heat produced by the welding process, lower carbon content produces the least carbide precipitation which may cause intergranular corrosion on stainless steel under some conditions. Therefore, the ability of intergranular corrosion resistance of 304L stainless steel is better than that of 304 stainless steel.
316L stainless steel, also known as titanium steel which is added 2~3% Mo, improving the stability of passivation film. 316L stainless steel is possessed with not only great pitting corrosion resistance and intergranular corrosion resistance but also good chloride resistance so that its corrosion resistance is much better than 304 and 304L stainless steel in marine condition or erosive industrial atmosphere.
In conclusion, from the perspective of corrosion resistance, 316L>304L>304. Low-carbon stainless steel is better than the normal stainless steel of the same steel series. Adding Ti or Mo or having solution treatment are major precautions of stainless steel pitting.
Effect of Corrosion on Austenitic Stainless Steel for Nuclear Power in Marine Condition:
Corrosion characteristics of the marine environment.
Under normal air condition or freshwater environment, stainless steel is to be corroded and form a layer of the dense oxide film which restrains the corrosive process on stainless steel.
It is of high chloride content in the air under the marine environment. Chloride ions easily replace oxygen ions in the oxide film, which destroys the oxide film, making it difficult to maintain in a stable passive state in an environment with a certain concentration of chloride ions.
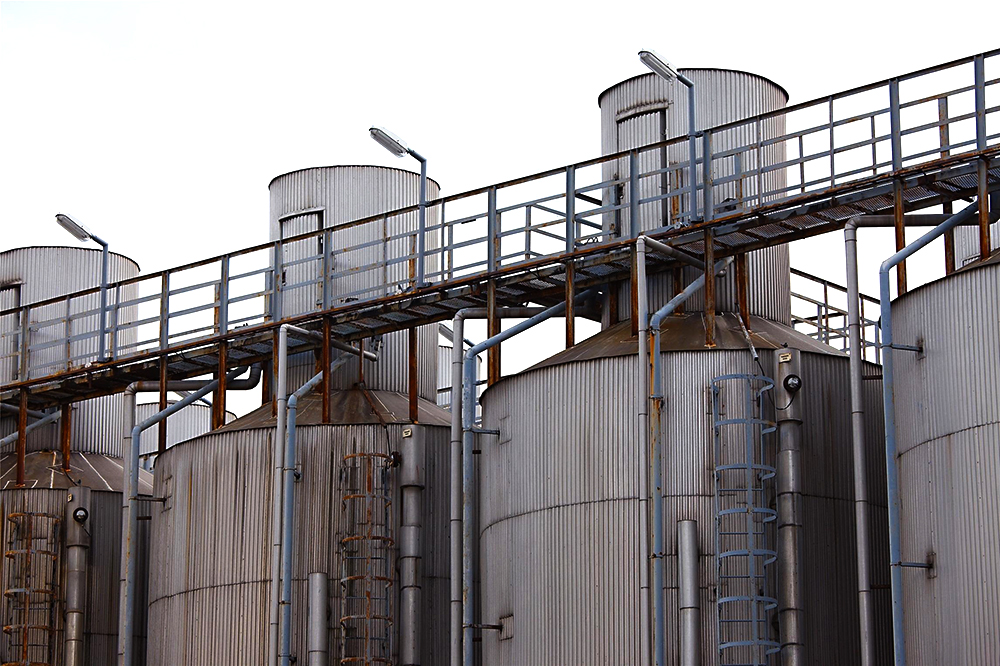
However, molybdenum in stainless steel can reduce the destruction of the passivation film caused by chloride ions. With the accumulation of chloride ions on the materials, the concentration is getting higher, causing larger corrosion to the stainless steel.
Pitting Corrosion
Pitting corrosion is small partial corrosion which is concentrated on the metal surface.
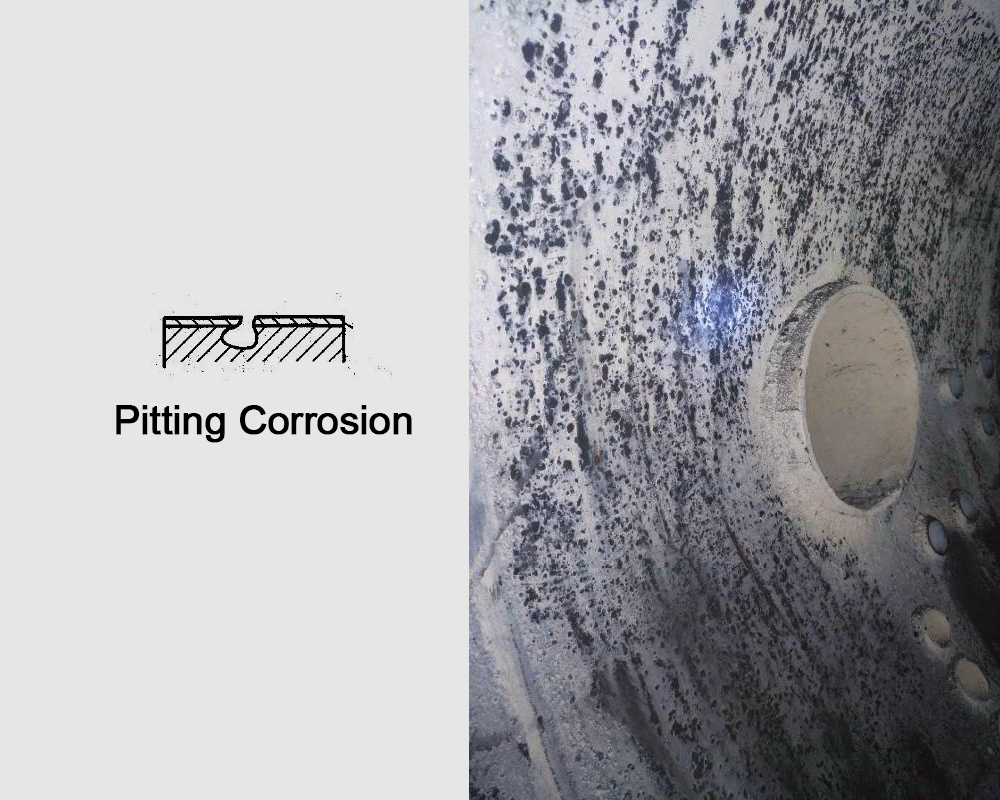
Before the pitting corrosion fully formed, there is a micro pit with a diameter of several micrometers in the protective oxide layer covering the surface of stainless steel. The rapid increase of such micro pits makes the reason for massive corrosion to the stainless steel.
After pickling the stainless steel on the surface, a CrO3 or Cr2O3 oxide film is formed, maximizing the ability of the corrosion resistance of stainless steel, restraining corrosion and destruction by the corrosive medium.
Generally, the corrosion of the stainless steel device of a nuclear power plant is pitting corrosion which arises mostly on the surface where the passivation film is damaged such as on gaps and scratches. If it is damp and includes chloride ions, it can form strong acid that dissolves the passivation film, imbalances the stability of the passive state, causing massive corrosion.
Intergranular Corrosion
Intergranular corrosion is a kind of common partial corrosion on metal. From the surface of the metal, along with the interface between the metal grains, the corrosion extends into the interior of the grains, weakening the combination between the grains.
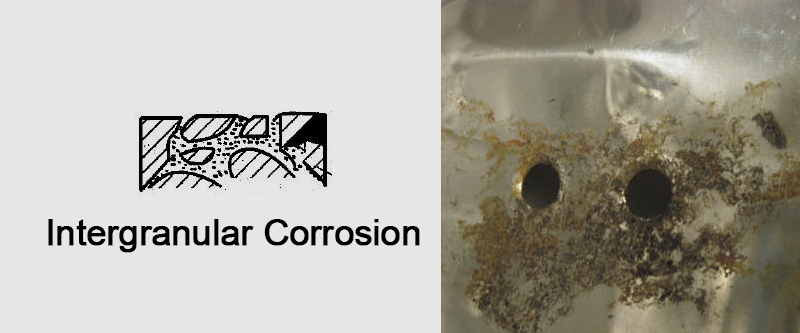
It is random corrosion that reacts along with the interface into the inner metal. There is no evidence can be noticed from the metal's surface, but it deprives the mechanical properties of the materials or even the material loses all the strength. Intergranular corrosion is one of the partial corrosion types that cause large damages.
With the ventilation purification system in long-time functioning, chloride ions accumulate to a certain extent and cause intergranular corrosion on the outer stainless steel. Stainless steel that is affected by this corrosion does not appear any damage or corrosion on the surface, but the grains inside the stainless steel has been damaged.
When the corrosion reaches a certain limit, it will cause damage to the devices and machines. In severe cases, it will affect the safe operation of the entire nuclear power plant.
Precaution of Corrosion
In the marine environment, humidity and salt content are high in the air. Chloride ions floating in the air is one of the major causes of stainless steel corrosion. Through researching the effects on Austenitic stainless steel in the marine environment and making comparisons among the functions of Austenitic stainless steel materials, to improve the ability of corrosion resistance of stainless steel materials, this article raises 5 solutions as below.
1. Pickling and passivating the surface of stainless steel.
By pickling and passivating, there will be a thin and dense passivation film covering the stainless steel, which separates the corrosive medium, forming basic protection of Austenitic stainless steel.
2. Avoiding the concentration of halogen ions.
Setting a dryer or mist eliminator at the air inlet of the ventilation system, reducing chloride content entering the ventilation system as much as possible, to lower the concentration of chloride ions that are attached on the stainless steel surface and lessen the corrosive extend of Austenitic stainless steel.
3. Installing a connector that adds passivator at the entrance of the ventilation system,releasing low concentration of nitrate or chromate to the ventilation system, to control the number of chloride ions attaching on the metal surface, preventing pitting corrosion and intergranular corrosion.
4. Choosing 316L stainless steel as much as possible.
Austenitic stainless steel containing 2~4% molybdenum is good at pitting corrosion resistance. Using this kind of stainless steel can significantly reduce pitting corrosion and intergranular corrosion.
5. Bright annealing.
It can improve the stability of passivation film under chloride ions environment and strengthen the ability of corrosion resistance.